Own a prefab home ‘on steroids’—on a modest budget
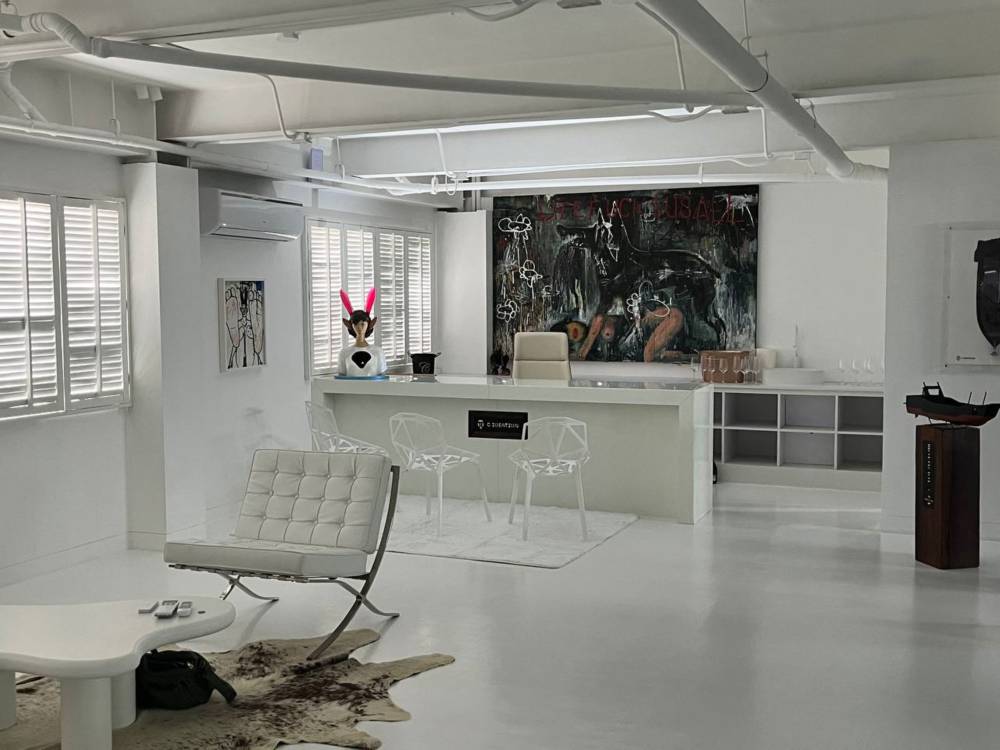
If you’re in immediate need of a shelter and have a modest budget, you can now order your dream home online from this innovative upstart. Simply provide a visual reference, and artificial intelligence will tailor the design and estimate the costs. Your new home can then be assembled on-site in just three to six months, complete with electricity and plumbing.
The Philippines faces a significant housing shortage, with an average of only 140,000 new homes built annually and a backlog of 7 million. This shortfall isn’t primarily due to a lack of funds, but rather a shortage of critical construction materials such as cement and steel.
Traditional homebuilding relies heavily on these materials, making homes bulky and expensive. As urbanization accelerates, the demand for land and construction materials surges, driving up prices. Moreover, the lengthy timelines, delays in materials, and high costs associated with conventional construction methods can be overwhelming for homeowners.
“The solution lies in using alternative materials and adopting a modular approach,” explains Jose Paolo (JP) Calma, founder and CEO of Homeqube. This company is dedicated to addressing the housing crisis through the application of smart technology, advanced materials, efficient design methodologies, and cutting-edge internet-based systems.
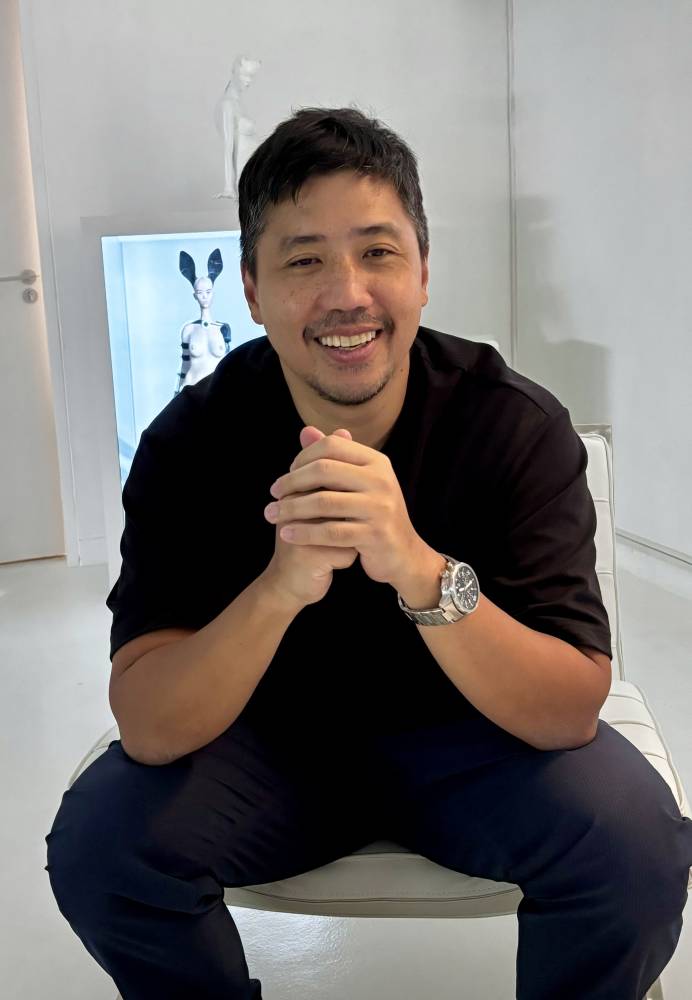
“Our primary strategy is to supply pre-built components for houses,” Calma explains. Similar to prefabricated homes, structures are assembled on-site after being manufactured in a factory. However, unlike traditional prefabricated homes which provide limited styles, Homeqube’s “built environment engine” offers virtually limitless design possibilities.
Like Lego
Homeqube started out two years ago as an online marketplace and producer of precast components with Calma and Filipino and Singaporean investors. While the main office is in Singapore, the showroom in Makati presents 45 scale models. Each is matched with a unique QR code that unlocks a world of customization options. A single scale model can be reconfigured to suit individual preferences, from exterior finishes to interior layouts.
“It’s like prefab on steroids or building with Lego, but on a much larger scale,” Calma adds. He assures that the construction process adheres to all Philippine building codes.
Homeqube’s online delivery service enables Filipinos to build homes on any type of land, from subdivisions to coastal properties and rural farms. The company handles the entire process, from securing permits to procuring materials and overseeing installation. This streamlined approach significantly reduces construction time, making homeownership attainable.
Homeqube provides the foundational framework using glass fiber reinforced polymer (GFRP), a corrosion-resistant material that replaces traditional steel rebars, and fiber metal laminates (FML), a lightweight yet strong structural reinforcement. Clients, often with the guidance of architects or contractors, can then order additional components such as doors, windows, and interior finishes.
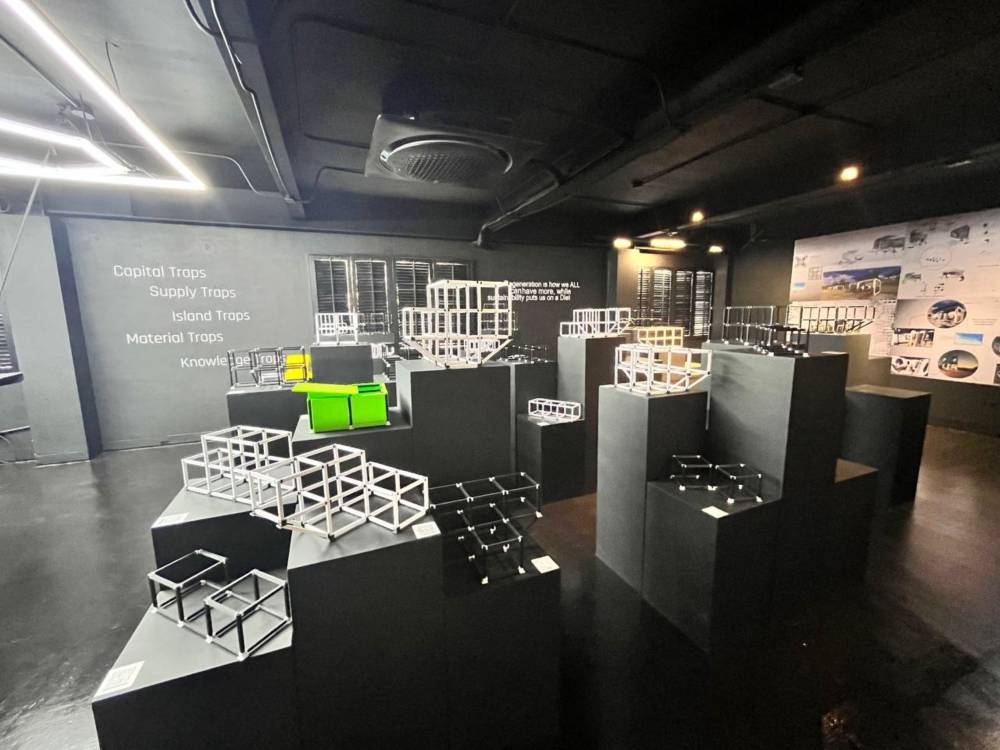
This approach is particularly well-suited for off-grid homes in remote locations, such as beaches, farms, or areas without readily available utilities. The project cost can range from P1 million to P15 million, significantly reducing labor costs and carbon footprint. These homes are designed to last for 50 years and can even be disassembled and relocated, unlike traditional concrete and steel structures.
“The goal of AI is to create affordable, livable homes,” Calma explains. “Homeowners have the flexibility to customize and replace parts as needed.”
However, he acknowledges that for those seeking architecturally significant or artistic homes, traditional construction methods might be more suitable.
Architect vs AI
Calma’s deep understanding of the construction industry stems from his family background. His father, Pablo, founded Multi-Development Construction Corp. (MDCC), specializing in hospitality projects. His brother, Carlo, is a prominent design consultant known for his avant-garde homes.
Having worked for MDCC since he was 16 and witnessing the challenges of conventional construction firsthand, Calma decided to disrupt the industry during the pandemic. He recognized the lengthy and costly nature of the traditional AEC (architecture, engineering, construction) process, which often takes an average of two years to complete in the Philippines. His strategy was to offer customized homes and buildings at a scale similar to mass production.
“I sought a lightweight material that could withstand our country’s typhoons,” Calma explains. “I discovered composite materials that were not only strong but also 70 percent more carbon-friendly. These materials can be assembled by a team of just five people, significantly reducing construction time compared to conventional methods.”
While architects typically design with a specific end goal in mind, Homeqube’s AI-powered system begins with a scale model and analyzes the behavior of different materials to generate various design possibilities.
“This approach allows us to explore multiple outcomes from different materials,” Calma notes. “Homeqube is not intended for masterpiece projects but rather for efficient and productive solutions to tackle the housing shortage.”
Homeqube’s showroom is at 1125 Antipolo St., Rizal Village, Makati, or visit www.homeqube .com, or contact 09621528796 or email peb@homeqube.com.