‘Mommy, how is this made?’
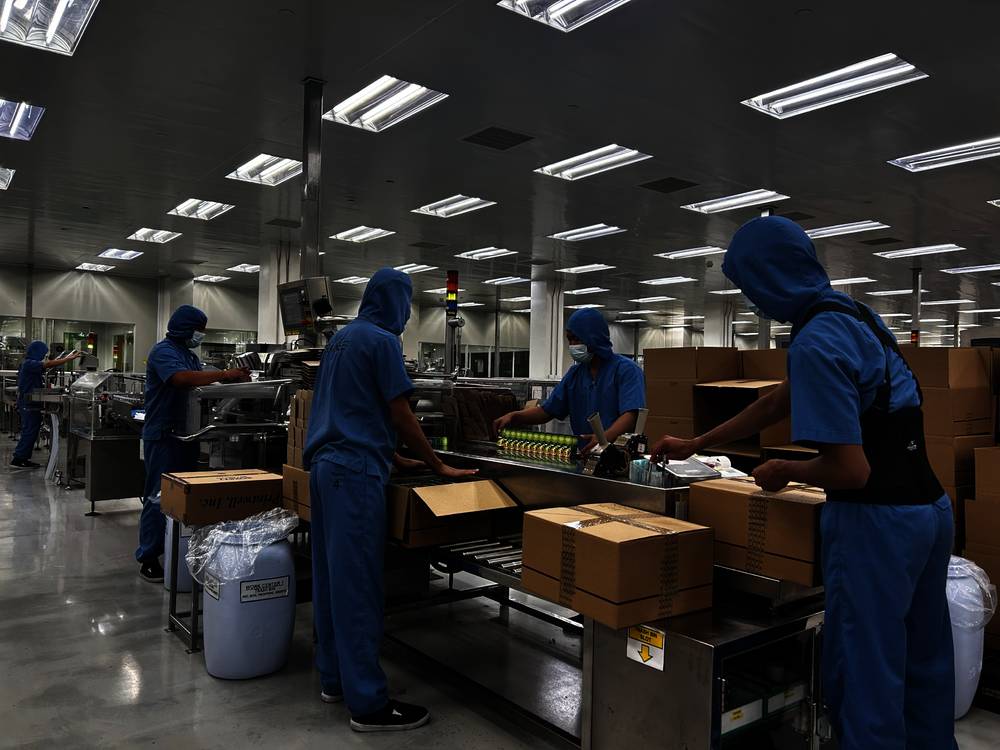
Mommy, how is this made?”
Lately, that has been one of my 6-year-old’s favorite questions about most things—appliances, furniture, clothes, toys.
My standard, nondescript reply: “Um, in a factory, baby.”
Thankfully, a recent tour of pharmaceutical company Unilab’s facility in Biñan, Laguna, has better equipped me to respond to her in more detail if and when she asks me how medicines are made. For a select group of members of the press, Unilab opened its laboratory, warehouse and distribution center, and gave us a crash course on their production and delivery processes, and the measures they take to ensure the quality of their brand.
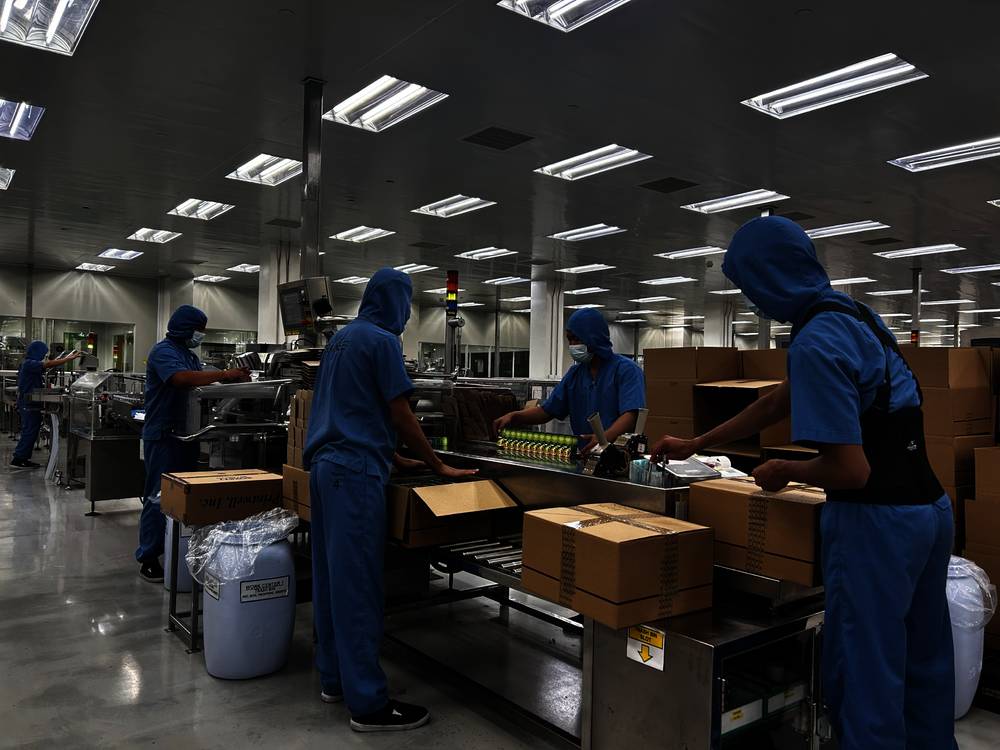
To start the tour, Unilab took us Gown Town—aka to the “gowning” station, where we were each given two sets of personal protective equipment (PPE). Since Amherst Laboratories is the center of all drug production, hygiene and cleanliness is of utmost importance; every day, employees first head into a locker room to change into a hooded scrub suit (color-coded based on one’s assigned location in the lab), put on shoe covers and a face mask, before heading up to the production floors.
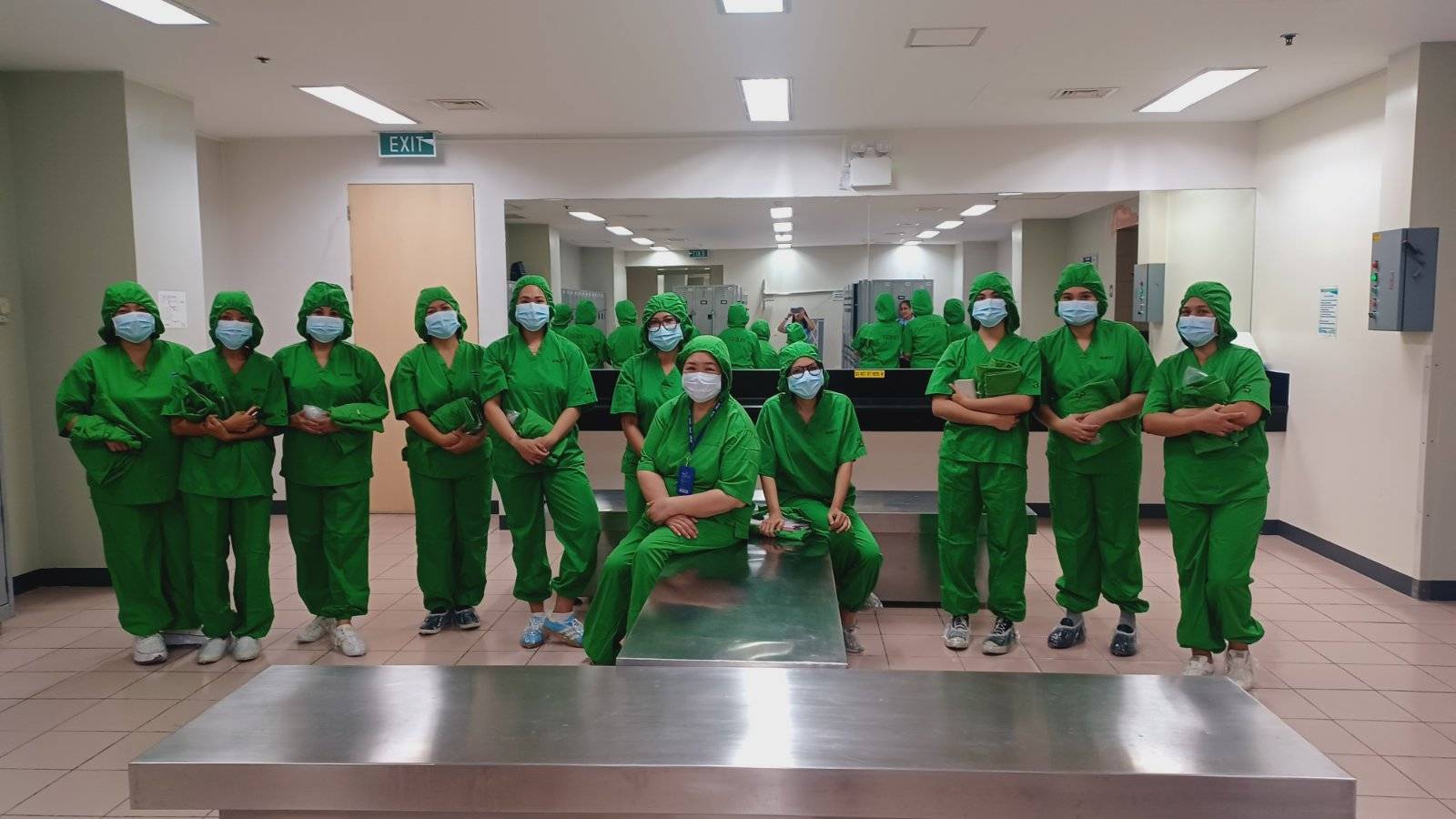
Once there, they reach a second locker room, where they put on a second protective coat (still hooded), and another set of shoe covers. Like them, our group all donned the same gear, and, after thoroughly washing our hands, entered the heart of the lab where they mix all the liquid medicines.
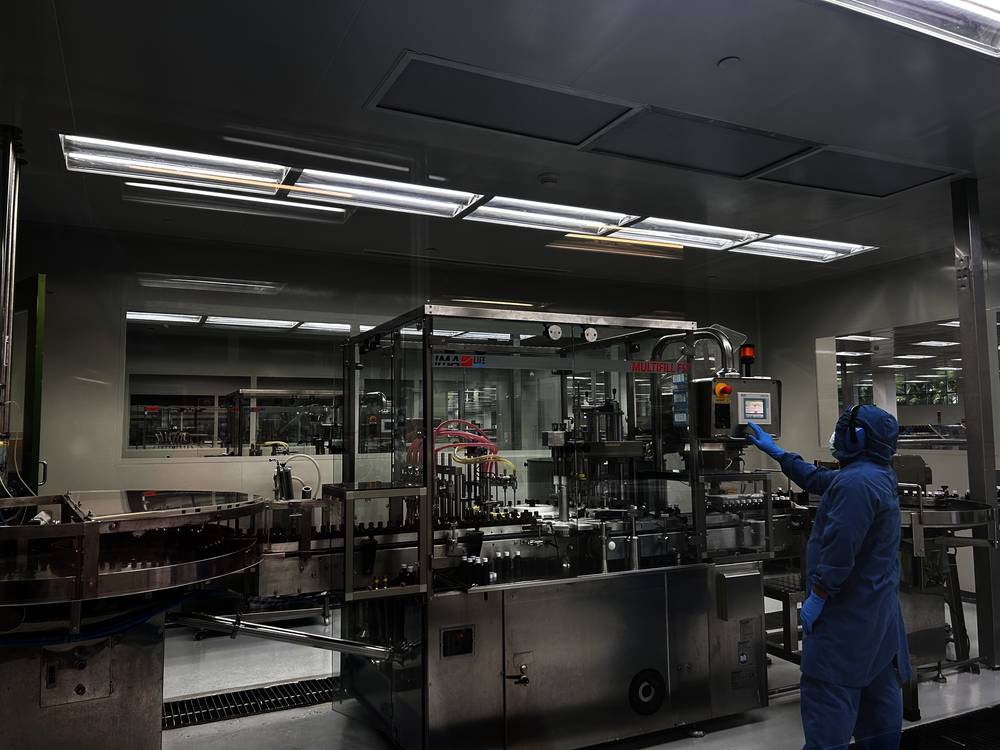
We were led to the Dispensing Station, where raw materials are delivered, and then mixed in large batches, following the formulas of the brands in production. From there, these batches are moved to the Processing Station, where they are placed in tanks almost 10 feet high. The tanks are all connected to Amherst’s computer systems, which automate the compounding of the liquid, before they are transferred to holding tanks prior to bottling. At the time, the tanks were filled with Solmux, which we got to see up close and personal, swirling in the holding tank.
Round-the-clock operations
Overseeing the entire process are chemical engineers who work in 12-hour shifts, ensuring operations run round-the-clock, which is crucial to the entire production. The backup generator, in fact, has its own backup, and the entire 45-hectares facility even has its own diesel supply.
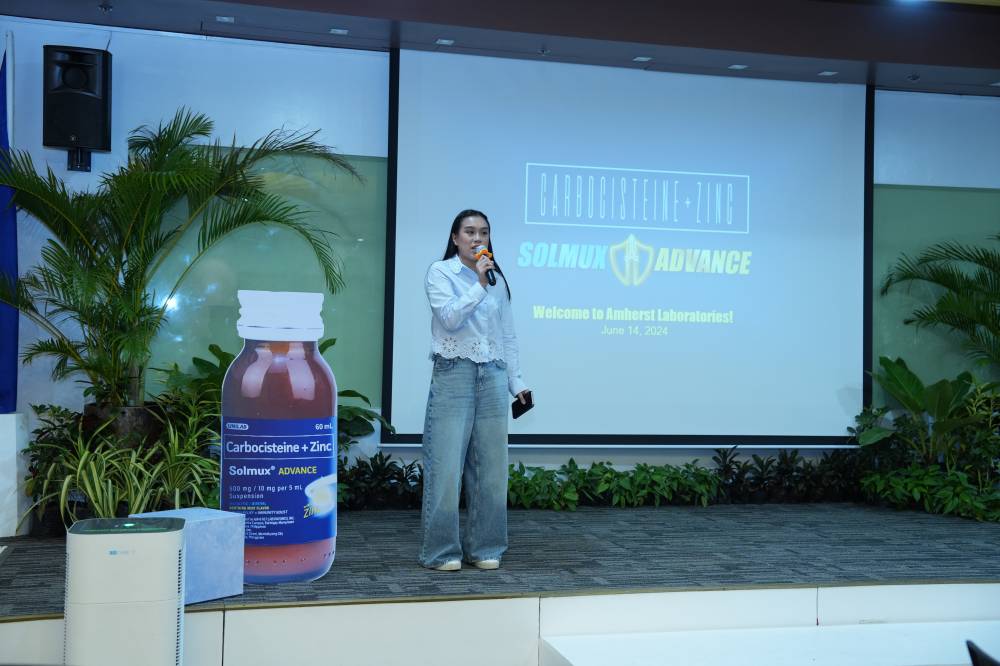
Before leaving the main production area, we removed our second-layer PPE and headed down to the packaging center, where we saw the Solmux being processed earlier now dispensed into the small bottles that would soon be delivered to pharmacies all over the Philippines. The packaging process itself has several steps: from bottle blowing to filling and capping, and then, finally, labeling and packing.
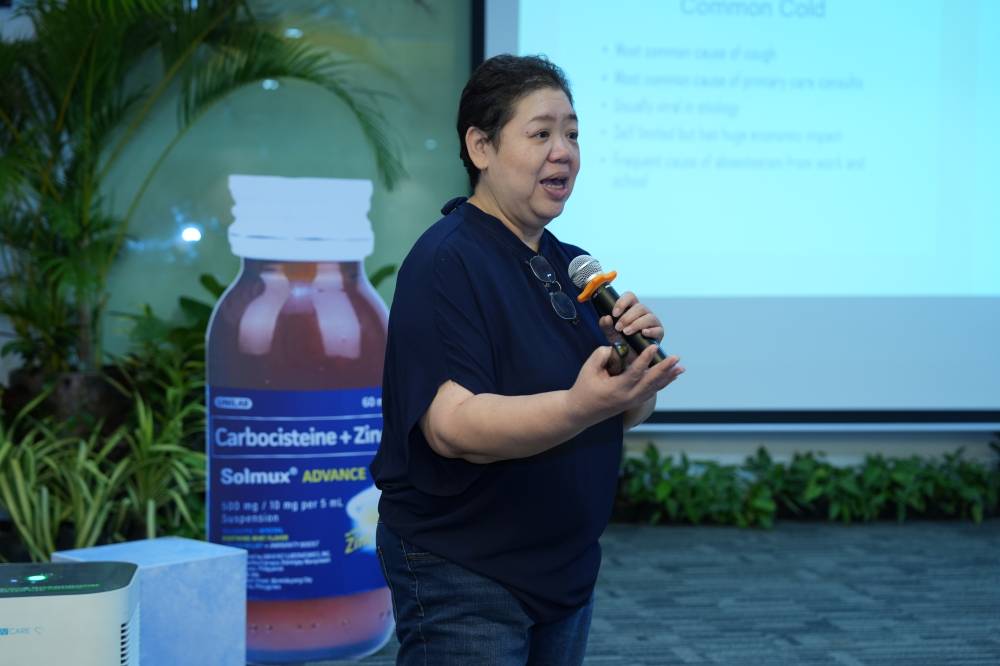
Unilab’s Biñan facility is the company’s central and single production and distribution hub that caters to all of its customers—a strategy that is not usually employed in the pharmaceutical industry, we were told by Albert Alcruz, logistics management assistant vice president of Unilab Inc.
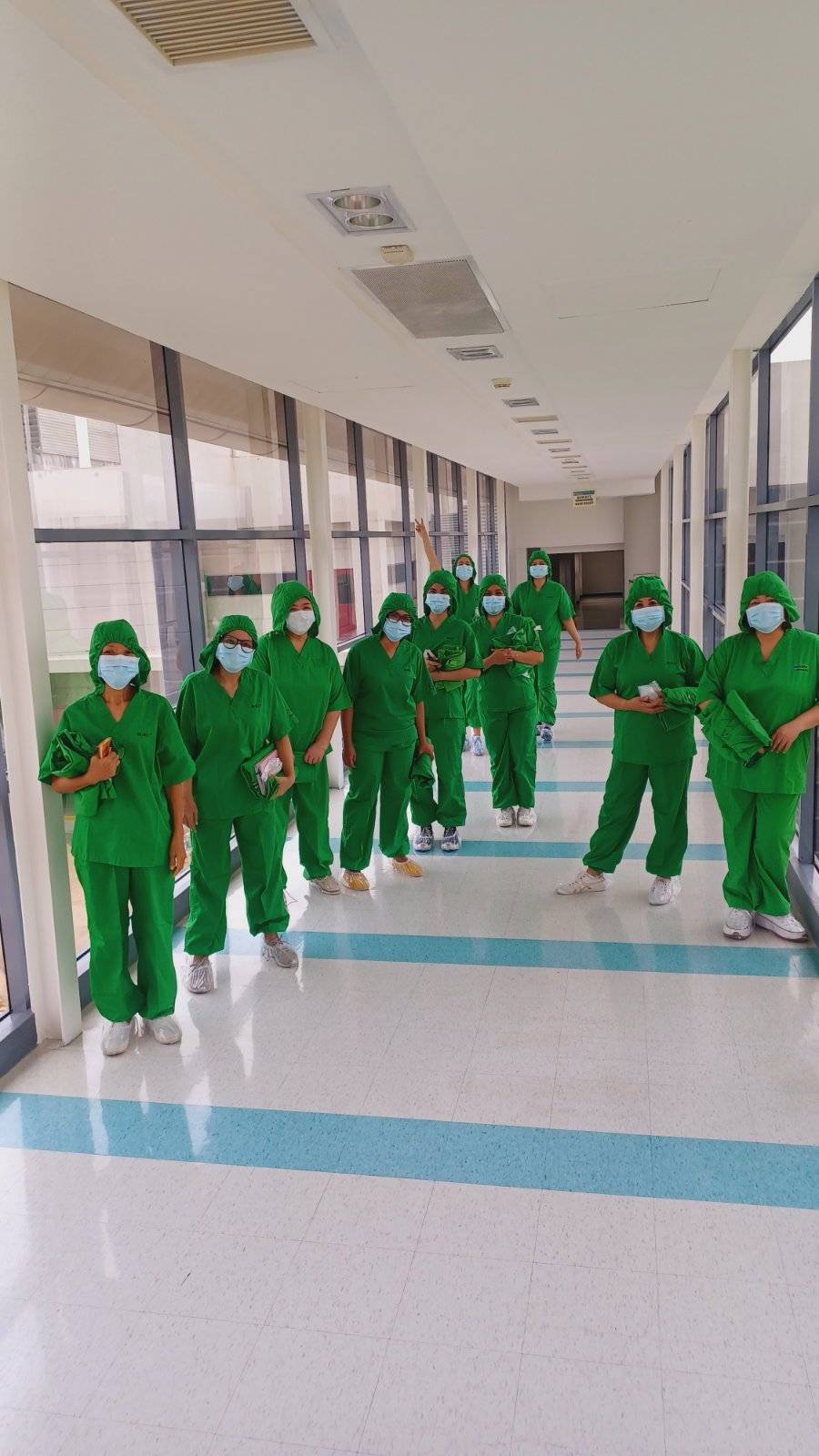
”Other companies typically have five, six centers across the country, but we decided to have one so that we could have better control of our inventory,” explained Alcruz. The warehouse and distribution center, under the brand First Pioneer Distribution Inc. (FPDI), are in a separate building, where we were asked to wear not PPEs, but hard hats—again, following the same safety protocol as the facility’s employees.
Quality control
Leo Atienza, operations senior manager of FPDI, conducted the tour of the building, where we first saw in action the tech behind their efficient fulfillment process: the company’s pick director, which automatically keeps track of all of the orders and where they need to go, and the status of stocks in the warehouse (including expiration dates).
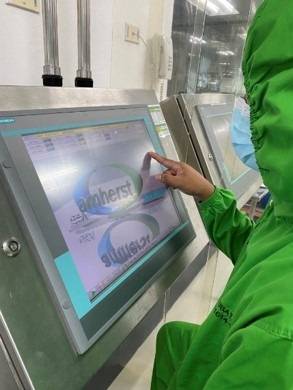
The system was designed specifically for the Filipino market, said Alcruz, so that Unilab could cater to even the smallest of pharmacies.
“We need to be flexible in order to truly fulfill the health needs of the Filipino people,” he added.
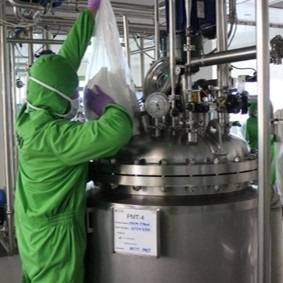
To further ensure that the quality of their products aren’t compromised, the medicines are placed in three different sections, depending on the temperature they need to be stored at: The largest is for those that need only to be at maximum 30 degrees Celsius; the next is for those that need to be at 25 C and below; and the last are for those that need to be at 2 to 8 C (we couldn’t stay too long in this area; none of us had thought to bring jackets).
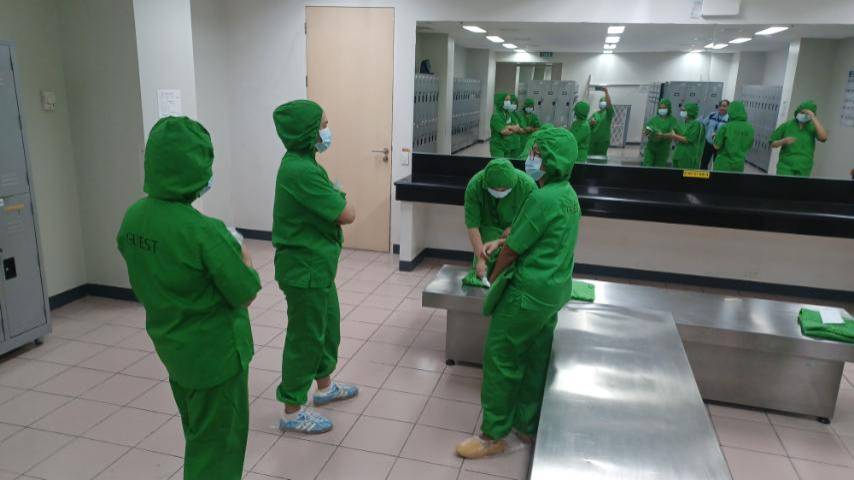
The tour ended with us exiting FDPI’s large hangar-shaped building (it can fit up to eight Boeing 747s!) through the loading docks where medicines are picked up by delivery trucks. All in all, it lasted three hours—and when I am asked by my daughter how her cough syrup was made, I won’t just have an answer; I’ll have a delightful bedtime story to share. —CONTRIBUTED