Silk production revival seen to meet ikat demand
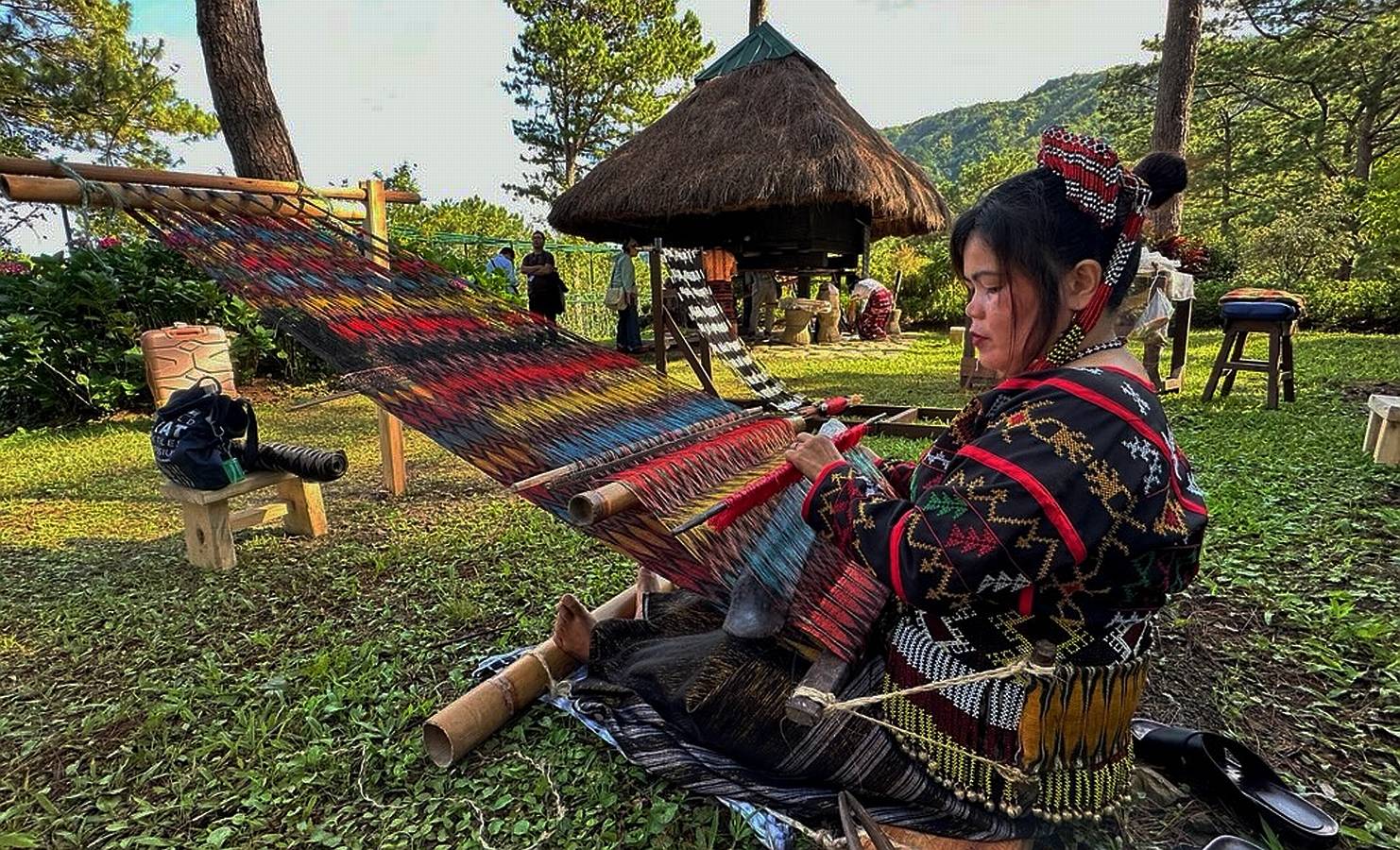
BAGUIO CITY—Domestic silk production is undergoing a revival in the provinces as international demand rises for natural dyes and indigenous fabric, experts said at this year’s World Ikat Textiles Symposium which was hosted by the Philippines for the first time in Baguio early this month.
Piloted 42 years ago in Benguet province, sericulture hubs have been put up in the Cordillera, Cagayan Valley, southern Luzon and Northern Mindanao where mulberry plantations again flourish, said Julius Leaño, director of the Philippine Textile Research Institute (PTRI), in a talk he gave at the symposium.
Sericulture or silk farming is a technology that cultivates silk from the cocoons of silk moth caterpillars which latch onto mulberry branches.
If the progress of mulberry silk farms continues as planned, the Philippines will be “silk sufficient” by the year 2030, employing 980 workers and earning P50 million in combined revenue, said Leaño, a published researcher specializing in textile chemistry.
But technology has afforded Filipino scientists the means to harvest weaving fiber from other plants as part of a government-led textile innovation drive, he said, with the development of yarns from bamboo, or “kawayarn,” water hyacinth, bakong (Hanguana malayana in Cagayan province) and the common “saluyot” (jute).
Some of these plants share the antimicrobial properties of yarn produced from pineapple, Leaño said.
Research into the potentially new plant sources for yarn coincides with new product lines using domestic woven fabric, such as ikat shoes, he said.
Ikat is a method of dyeing or coloring fabric in patterns before it is woven.
Preservation
Leading textile scholars like Joseph Lo of Singapore, Maria do Ceu Lopes da Silva of Timor Leste, Bina Rao of India and Mexican artisan Arturo Estrada Hernandez outlined ikat’s market growth and subsequent debates about authenticity among weaving cultures throughout the world.
National Living Treasures Samporonia Madanlo and Barbara Ofonga, who champion traditional Tboli weaving, and Rosie Sula for Tboli chant were vocal about the way commerce has upended efforts to preserve their ikat traditions, which are tied to the culture’s spiritual roots.
Indigenous ikat is generally woven by hand using handlooms, footlooms or backstrap looms and may take weeks or months to complete.
But one of the biggest obstacles being solved by government sericulture initiatives is the supply of indigenous dyes and textiles, which has not helped efforts to keep the weaving knowledge alive among present-day indigenous Filipinos, according to University of the Philippines (UP) Baguio anthropology professor Analyn Salvador Amores.
Amores heads the multidisciplinary program Cordillera Textiles Research Project (Corditex) of UP Baguio which has discovered and analyzed extant weaving techniques that are being reintroduced to Cordillera weavers who have long forgotten them.
Corditex identified the chemical makeup of dyes used by Itneg weavers in Abra, tracked down the original plants and other botanical resources used to produce woven Cordillera garments, and even studied the music, diagrams and mythology associated with the old handloom weaving traditions.
Amores said Corditex was also studying the region’s “textile value chain,” focusing on how the market, the local economy and the dwindling supply of raw materials had affected livelihoods and the protection of indigenous traditions when she first discussed the matter at the Cordillera Regional Handloom Conference in July.
The full revival of the government’s sericulture program was institutionalized in Benguet back in 2015, alongside mulberry farms in Kalinga and Misamis Oriental provinces, according to PTRI senior researcher Cheryl Lopez at the July forum.
Between 2017 and 2023, mulberry plantations had expanded by 1,563 percent, with silk cocoon production rising by 278.67 percent and raw silk production hiking by 760 percent, PTRI had said.