Ayala Land leads the way toward net zero, circularity

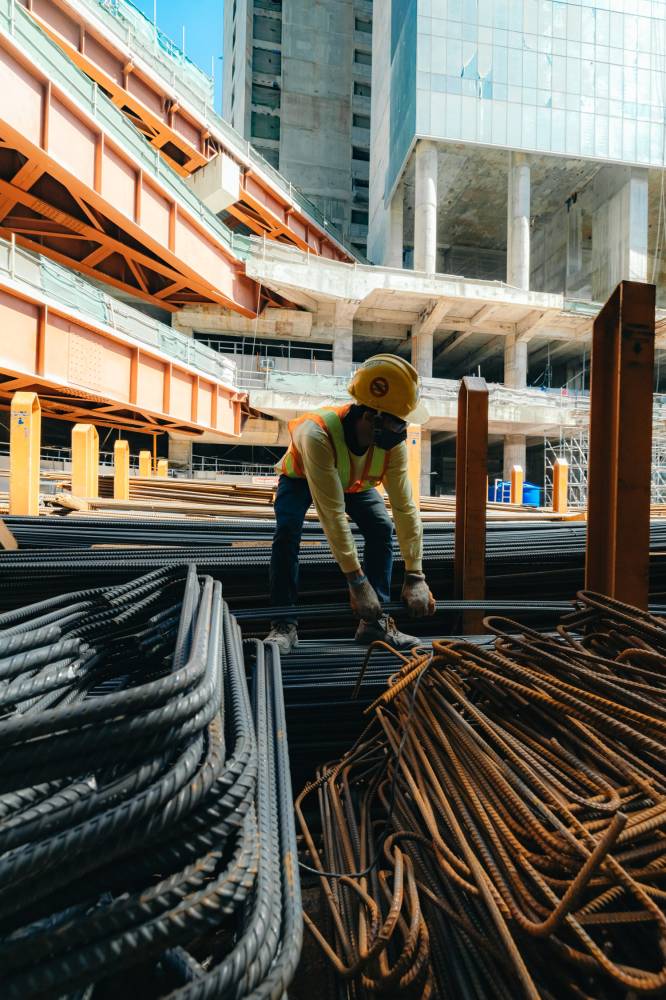
Imagine a future where homes and cities are not only built for comfort and efficiency, but also consider their impacts to the environment.
This is rapidly becoming a reality with the innovative efforts of Ayala Land, Inc. (ALI). The property giant is committed to creating quality developments while leading the charge in sustainability through resource efficiency, waste management and sustainable procurement, as part of its circular economy and net zero goals.
Ayala Land aims to reduce its greenhouse gas emissions to achieve its net zero 2050 targets. This commitment is reflected in every aspect of its business, from planning and development to construction and operations through pioneering initiatives, some of which are a first in the Philippines.
Examples of the activities being implemented by the company include shifting to renewable energy sources, integrating efficient resource management solutions in the properties and decarbonization strategies within the supply chain.
Sustainable Construction in Action
Ayala Land’s construction arm, Makati Development Corp. (MDC) is leading several initiatives aimed at sustainable construction. This focus is vital as MDC accounts for about 75 percent of Ayala Land’s total baseline GHG emissions, which were estimated at 2.9 million tons of carbon dioxide equivalent (tCO2e) in 2021.
“MDC is one of the largest construction companies in the country. This means we are best positioned to raise the capabilities and the standards in the industry—in innovation, automation, use of technology and AI. It is not enough just to be better at how we currently do things. We need to think about how to do things differently to deliver quality consistently and efficiently,” said Ayala Land president and CEO Meean Dy.
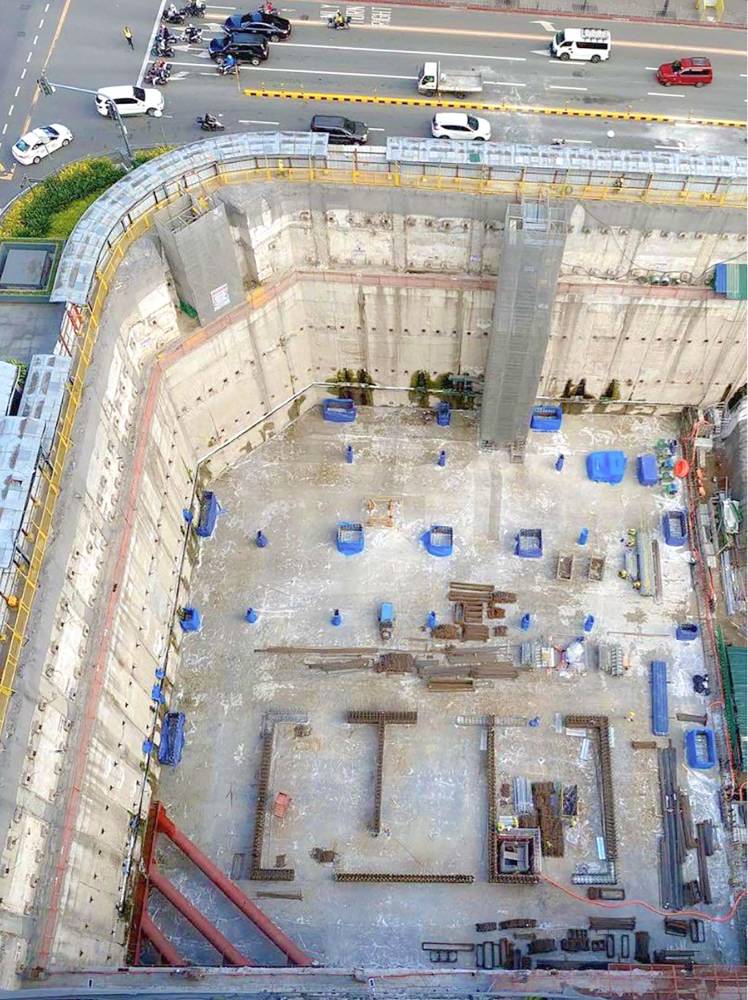
Net Zero Roadmap
Like its parent firm, MDC has also set an ambitious goal to reduce GHG emissions and achieve net zero by 2050. To achieve this, the country’s leading engineering, procurement, and construction company has rolled out initiatives to reduce emissions under Scope 1 and 2.
These include its electric vehicle re-fleeting program to reduce use of fossil fueled cars; reforestation activities in Ayala Land’s carbon forests; use of the latest solar technologies; pre-fabrication and modular construction technologies; and MDC’s Corporate Center shift to renewable energy via the Green Energy Option Program (GEOP) which is expected to result in an annual reduction of 222.49 tons of carbon dioxide equivalent.
Greening the Supply Chain
What’s highly crucial, and probably most difficult as well, is reducing GHG emissions under Scope 3—the emissions from upstream and downstream activities in the company’s value chain.
At present, 99.2 percent of MDC’s emissions fall under Scope 3. Since this involves MDC’s suppliers, significant efforts will be needed to engage partners to fully green the supply chain.
MDC, however, is fortunate to have partners who also believe in the value of going green and decarbonizing.
The construction unit earlier partnered with cement maker Holcim Philippines for a research and development project that would zero in on reducing carbon emissions.
In February this year, Ayala Land, MDC, and SteelAsia Manufacturing Corp. signed an agreement to collaborate on decarbonization action plans such as the recycling of metal scraps into rebars (steel reinforcing bars). This would not only lower project costs, but also mitigate negative impacts to the environment.
“As an application of circular economy principles, we partnered with SteelAsia Manufacturing Corp. to supply MDC with rebars recycled from metal scraps generated by our construction projects. This agreement is the first of its kind in the country,” Dy explained.
As of April, MDC has purchased 3,876 metric tons (MT) of steel with recycled billets dubbed as green steel, which equates to avoiding emissions of 7,870 tons of carbon dioxide equivalent. According to MDC, green steel is estimated to have lower carbon emissions by as much as 87 percent compared to the conventional steel rebar.
Innovations on low carbon materials
Other innovations include the use of low carbon concrete, fly ash and slag as cement alternatives, and recycled PET materials as concrete additives.
“MDC is the largest producer of low carbon concrete in the country. This concrete mix which uses alternative materials results in 24 percent lower carbon emissions versus conventional concrete mixtures. This was used in the concrete works and foundation of the new BPI headquarters, currently under construction in Makati,” Dy said.
The glass fiber reinforced polymer (GFRP), which is composed of a polymer plastic matrix with embedded glass fibers, is meanwhile used for pre-cast walls, slab on grade, sewer manhole covers along sidewalk, area drain, curb and gutter, among many others. GFRP’s carbon emission is estimated to be 43 percent lower compared to conventional steel.
Circularity in Construction
Circularity is another key sustainability target for the company.
MDC practices circularity by reusing metal scraps for rebars and incorporating recycled content in cement. MDC also uses construction materials made with plastic wastes collected from Ayala Land properties. These eco-materials include pavers for sidewalks, board-up and fencing materials.
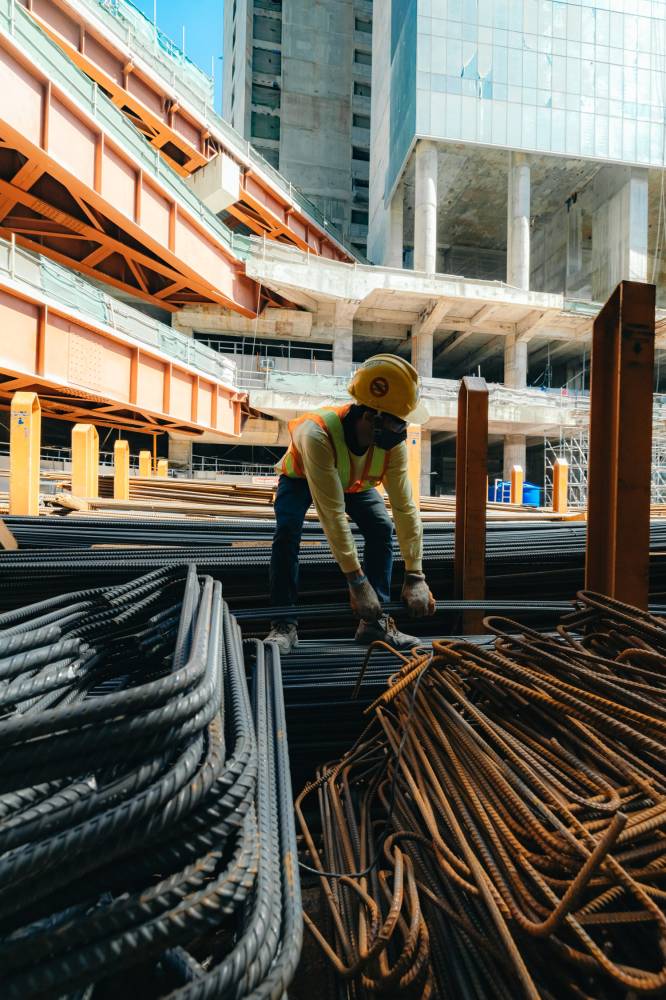
MDC’s programs do more than just reduce resource extraction and lower carbon emissions. They also divert substantial amounts of waste from landfills, illustrating a practical application of circular economy principles.
By ensuring that resources are sustainably used in a continuous loop, Ayala Land and MDC are setting new standards for the construction industry.
Step by Sustainable Step to 2050
“MDC’s vision for the future includes a heightened commitment to responsible building. We recognize the importance of protecting our planet and are dedicated to integrating sustainable solutions into our operations,” MDC president Dan Abando said.
“We will do this by supporting Ayala’s Net Zero Greenhouse Gas Emissions by 2050 Vision through interventions such as decarbonization, circularity, supply chain engagement, and the use of sustainable materials for our construction operations,” he added.
But this is just the start, more initiatives and innovations are set to be rolled out in the coming years, leading up to 2050. This includes the gradual adoption of electric vehicles for service vehicles and construction equipment, the phasing out of internal combustion engine vehicles and equipment, and the construction of net zero buildings.
By leading the charge in transforming the construction industry, Ayala Land and MDC are setting an example for others to follow.
Through their innovative efforts in resource efficiency and circularity, they are not just building structures, but also paving the way for a greener, more sustainable future, taking concrete step by sustainable step.
